Find best Cement Suppliers for all your bulk order needs
We connect buyers to top Cement Suppliers, helping both find the right match for their needs.
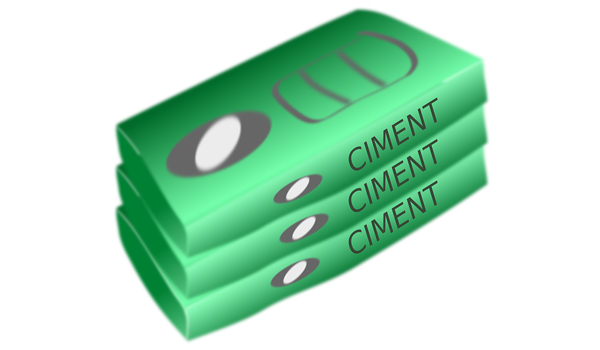
Browse Cement products at wholesale price from the best Cement suppliers
Looking for a supplier of Cement at wholesale prices? Look no further! Post your requirements and get best deals on Cement for your business from multiple Cement suppliers.
White Tiles Adhesive
lajai chokdi morvi rajkot highway, Morvi, Gujarat, 363642, India
Terracotta Tiles Adhesive
lajai chokdi morvi rajkot highway, Morvi, Gujarat, 363642, India
Wonder Xtreme
Price : Rs 335 / Bag
PLOT NO. 11, S.NO. 59, DATTA COLONY, SWAMINARAYAN MANDIR ROAD, NEAR SHREE RAM CHOWK, DEOPUR, DHULE - 424002, Dhule, Maharashtra, 424002, India
Wonder PPC
Price : Rs 450 / Bag
PLOT NO. 11, S.NO. 59, DATTA COLONY, SWAMINARAYAN MANDIR ROAD, NEAR SHREE RAM CHOWK, DEOPUR, DHULE - 424002, Dhule, Maharashtra, 424002, India
Premium+ Quality PSC Cement (Fly Ash Addition)
137, Swamiji Sarani Road Patipukur, Kolkata, West Bengal, 700048, India
Portland Pozzolana Cement [SLAG Based]
137, Swamiji Sarani Road Patipukur, Kolkata, West Bengal, 700048, India
Portland Pozzolana Cement [Fly Ash Based]
137, Swamiji Sarani Road Patipukur, Kolkata, West Bengal, 700048, India
All Variety of Cement
Khetrapatna ,murgabadi , Baripada Town, Odisha, 757081, India
Cement
Explore Cement related category & post requirement to connect with Cement related suppliers for your bulk order needs and get the best deal on high-quality Cement related products at wholesale price.
Cement:
Cement is a substance that is used as a binder for construction. It sets, hardens, and get fixed to other materials to bind them together.
Usually it is used to bind sand and gravel (aggregate) together.
Some facts about Cement:
- Cement is one of the the basic ingredient of concrete which is the most widely used material in existence and is formed when portland cement is mixed with water to create a paste that can bind with sand, brick and rock to harden.
- A closely controlled chemical combination of calcium, silicon, aluminum, iron and other ingredients is used in the manufacturing of cement.
- Limestone, shells, and chalk or marl are the common material that is combined with shale, clay, slate, blast furnace slag, silica sand, and iron ore to manufacture cement.
- These ingredients are heated at high temperatures to form a rock-like substance which will be ground into the fine powder to form cement.
Types of Cement:
Cement is a prime component of any construction work that forms a high percentage of overall costs. Therefore, it is important to choose the right one from the different types of cement. Cements used in construction are often lime or calcium silicate based and is usually inorganic. Cement can be characterized as non-hydraulic or hydraulic depending on the ability of the cement to set in the presence of water.
Non-hydraulic cement:
- Cement that does not set in wet conditions or under water is non-hydraulic. It reacts with carbon dioxide in the air and sets as it dries.
- Non-hydraulic cement is resistant to chemical attack after setting.
Hydraulic cements:
- Hydraulic cements set in wet conditions or under water and become adhesive due to a chemical reaction between the dry ingredients and water.
- Mineral hydrates are formed due to chemical reaction which are not very water soluble. Therefore, these are quite durable in water and safe from chemical attack.
- Volcanic ash (pozzolana) with added lime (calcium oxide) were used by ancient Romans for the manufacturing of hydraulic cement.
Portland Cement:
- Portland Cement, a form of hydraulic cement is the most common type of cement that is used around the world.
- Portland cement was first made by Bricklayer Joseph Aspdin of Leeds, England early in the 19th century by burning powdered limestone and clay in his kitchen stove
- Portland cement is the basic ingredient of concrete which is formed when a paste is created with water and portland cement that binds with sand and rock to harden.
- Usually it is made from limestone with a basic ingredient of concrete, mortar, stucco, and non-specialty grout.
- Limestone and clay minerals are heated in a kiln to form clinker and then the clinker are grinded and added to 2-3 percent of gypsum to produce a fine powder.
- Ordinary portland cement (OPC) is grey in color and is the most common type of Portland Cement. However, white portland cement is also available which is almost similar to ordinary, grey, portland cement in all respects, except for its high degree of whiteness.
- The method of manufacture to obtain this white color requires high purity raw materials with low Fe2O3 content. A higher kiln temperature is also required to sinter the clinker in the absence of ferric oxides.
- White portland cement is more expensive than the grey cement as it requires a higher sintering temperature around 1600 degree centigrade because Fe2O3 decreases the melting point of the clinker.
- Portland cement can cause chemical burns as it is caustic. It can also cause irritation or lung cancer with severe exposure as it contain a number of hazardous components, including crystalline silica and hexavalent chromium.
- High energy consumption is required to mine, manufacture, and transport portland cement which is the main concern for environment.
- Air polution can be caused by the release of the greenhouse gas carbon dioxide, dioxin, NOx, SO2, and particulates.
- Portland cement is not very expensive because of widespread availability and low cost limestone, shales, and other naturally occurring material used in it.
- The clinker of portland cement is a hydraulic material that consist of hydraulic calcium silicates containing one or more of the forms of calcium sulfate.
- Portland cement is commonly used in the production of concrete which can be used in the construction of structural elements like panels, beams, and street furniture.
- The product sets in a few hours, and it takes some weeks to harden when water is mixed with portland cement.
- Severe skin burns can occur with wet cement if not promptly washed off with water as it is strongly caustic.
- Severe eye or respiratory irritation can be caused by dry cement powder in contact with mucous membranes.
- Each step in the manufacture of portland cement is checked by frequent chemical and physical tests in Cement plant laboratories.
- The finished product is also analyzed and tested to ensure that it complies with all industry specifications.
Manufacturing of Portland Cement:
- Most commonly the dry method is used in the manufacturing of portland cement.
- The first step in the manufacturing of portland cement is to quarry the principal raw materials, including limestone, clay, and other materials.
- The rock is crushed after quarrying which involves several stages.
- The rock will be reduced to a maximum size of about 6 inches in the first crushing. Then it goes to secondary crushers or hammer mills for reduction to about 3 inches or smaller.
- The crushed rock is then combined with other ingredients such as iron ore or fly ash and is ground, mixed, and fed to a cement kiln.
- All the ingredients are heated to about 2,700 degrees Fahrenheit in large cylindrical steel rotary kilns lined with special firebrick in the cement kiln.
- The slurry or the finely ground raw material is fed into the higher end.
- A roaring blast of flame is produced by precisely controlled burning of powdered coal, oil, alternative fuels, or gas under forced draft at the lower end.
- Certain elements are driven off in the form of gases as the material moves through the kiln.
- The remaining elements unite to form clinker which comes out as grey balls, about the size of marbles from the kiln.
- Clinker is discharged red hot from the lower end of the kiln and is generally brought down to handling temperature by using various types of coolers.
- The heated air from the coolers is returned to the kilns, that saves fuel and increases burning efficiency.
- Cement plants grind it and mix it with small amounts of gypsum and limestone after the clinker is cooled to form a fine powder.
- The powder is now ready for transport to ready-mix concrete companies and can be used in a variety of construction projects.
- A wet process can also be used in the manufacturing of portland cement in which the raw materials are ground with water before being fed into the kiln.
Portland Cement Blend:
Different types of Portland cement blend are:
PSC Cement:
- PSC Cement, also known as Portland Slag Cement, is blended cement which is created with a combination of up to 45 to 50 percent of slag, 45 to 50 percent of clinker, and 3 to 5 percent gypsuma. Slag is an non-metallic product that consist of more than 90 percent glass with silicates and alumino-silicates of lime.
- Usually, PSC is lighter in color than OPC due to presence of slag.
- PSC cement has several advantages over ordinary cement because of its chemical composition.
- Ultimate compressive strength can be provided and excellent resistance can be offered to chloride and sulphate attacks apart from being eco-friendly.
- The risks of cracking can be lowered, shrinkage cracks can be minimized and workability can be improved because of its resistance to chloride and sulphate attacks.
- PSC cement can be used for all types of residential and commercial projects as it provides a superior finish.
- It is mostly used for marine constructions such as on dams and other water retaining structure due it is high resistance alkali-silica reactions and fewer shrinkage cracks.
- Ultimate compressive strength, low risk of cracking, improved workability, better compatibility with all types of admixtures, excellent resistance to Chloride and Sulphate attacks, superior finish, ease of pumping, better resistance against alkali-silica reaction and minimized shrinkage cracks are some of the advantages of PSC Cement over other type of cement.
- PSC can be used for plastering low rise residential building and is the most suitable cement for mass concrete applications, high performance or high strength concrete, structures and foundations, concrete pavements, pre-cast concrete such as pipe and block, concrete that are exposed to sea water and marine application.
- Its structural stiffness can be enhanced and load deflections can be minimized because it has higher flexural strength to concrete.
- PSC is more expensive than OPC in the market due to its improved properties.
PPC Cement:
- PPC Cement, also known as Portland Pozzolana Cement is manufactured by grinding Portland cement clinker, gypsum and a Pozzolana such as fly ash together.
- PPC is a blended cement that consist of 15 to 35 percent of pozzolanic material, 4 percent of gypsum and clinker.
- PPC cement is different from other type of cements as Pozzolana is added in the manufacturing process.
- Fly ash sourced from thermal power plants is the most common source of Pozzolana which reacts with moisture to form compounds that provide additional strength in PPC cement.
- PPC is usually darker in color than OPC because of the presence of fly ash.
- Higher resistance to water, easier to work with on site, lower heat of hydration and improved resistance to chemicals are some of the benefits of PPC.
- Portland Pozzolana cements has less initial setting strength but it hardens over time.
- PPC cement is used to protect the concrete against alkali aggregate reaction.
- It is suitable to be used in applications like masonry mortars and plastering because of its durability and workability.
- PPC cement is used in the construction of hydraulic structures, marine works, mass concreting etc.
- The manufacturing process of PPC cement is difficult. However, the cost of PPC is less compared to OPC.
- PPC cement is used in producing highly durable concrete as it has low water permeability compared to OPC.
OPC Cement:
- OPC Cement, also known as Ordinary Portland Cement is manufactured by mixing limestone and other raw materials consisting of argillaceous, calcareous and gypsum.
- OPC Cement the most widely and commonly used cement where there is a need for fast construction and setting time as it is the basic form of cement made up of 95 percent of cement clinkers and 5 percent of gypsum.
- It is commonly used in industrial and large construction as high compressive strength at early stages can be provided.
- OPC 33, OPC 43 and OPC 53 are the three grades of OPC Cement based on the compression strength (Mpa) of the concrete that will attain after 28 days of setting.
- OPC-33 Grade can only be used for low strength works like plastering as it attain a compression strength of 33 Mpa in 28 days of setting.
- OPC-43 Grade is widely used in non-RCC works, pathways and wall plastering, as 43 Megapascals of compression strength can be achieved in 28 days.
- OPC 53-Grade is recommended for all kind of house construction as per IS standard. It is also mostly used in RCC structures, buildings, pre-stressed concreting as a compression strength of 53 Megapascals can be achieved in 28 days.
- OPC 53-Grade cement can be used by partially replacing it with 20 percent of fly ash by the weight of cement in the construction site which not only saves cost but also improves the durability of cement as the pore refinement can be achieved by adding fly ash.
- Workability and strength can also be increased by partial replacement of cement by fly ash
- OPC cement is widely used for the construction of dams, high rise buildings, bridges, flyovers, roads where fast setting and high strength is required.
- The manufacturing process of OPC Cement is easy and is expensive than PPC cement.
- Resistance to sulphate attacks can not be provided by using OPC Cement.
- OPC cement dries more quickly then other type of cement as it attains strength in a shorter time. However, it gains strength during chemical reaction as more heat is produced.
White Cement:
- White Cement, also known as white ordinary portland cement (WOPC) is almost similar to ordinary, grey, portland cement in all respects, except for its high degree of whiteness.
- White Cement is more expensive than the grey cement as it requires a higher sintering temperature around 1600 degree centigrade as Fe2O3 decreases the melting point of the clinker.
- A combination of white aggregates with white cement can be used to produce white concrete for prestige construction projects and decorative work by using.