Warehouse Management
Updated: December 8, 2024
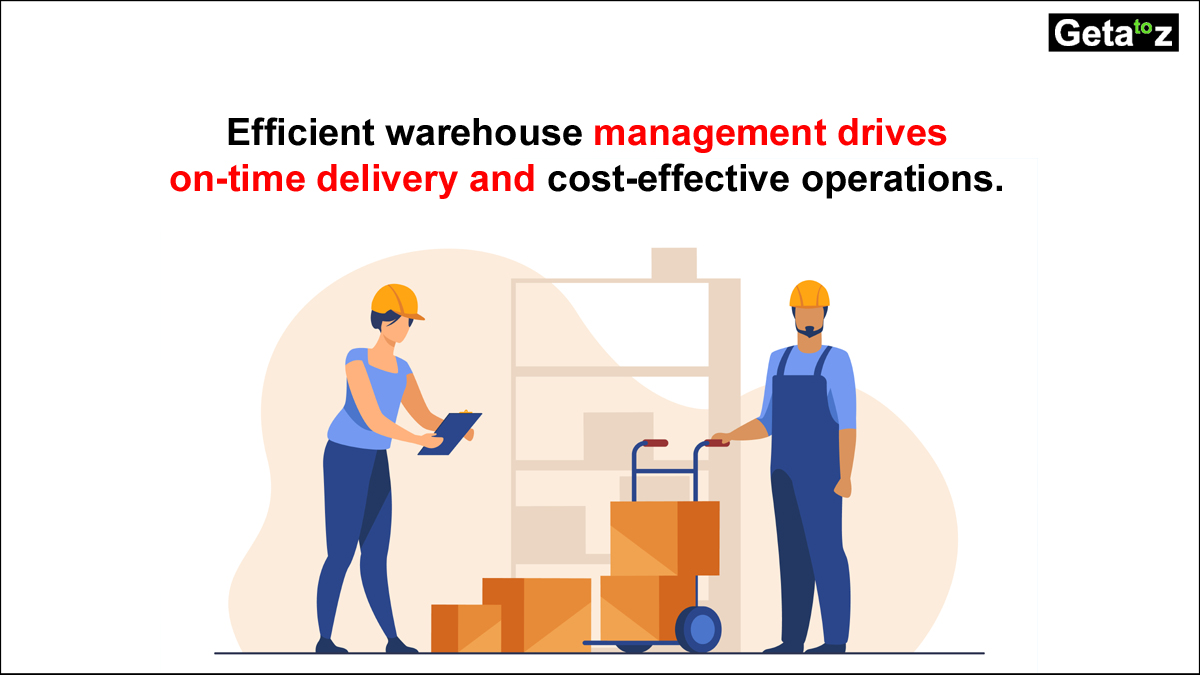
What is Warehouse Management?
When selling goods, storing them between orders is essential unless you're dropshipping. Typically, this storage is handled by a warehouse or fulfillment center. Without a well-organized warehouse, fulfillment delays are likely, leading to customers receiving incorrect, delayed, or missing orders due to confusion during stock receiving, storage, and retrieval processes.
Effective warehouse management ensures a smooth flow of stock into and out of the warehouse. It streamlines the entire process, which can otherwise become complicated with inbound and outbound logistics, especially for growing businesses. Warehouse management, or warehousing, covers every aspect of fulfillment, including tracking, storing, picking, packing, receiving, and shipping inventory.
The key goal of warehouse management is to ensure all operations within the warehouse function cohesively. It involves inventory planning, workflow design, staff training, and performance monitoring. Both large and small businesses benefit from it by overseeing their fulfillment processes, identifying issues, and implementing solutions without disrupting the flow of goods.
- Improved customer satisfaction: Warehouse operations have a visibly positive impact on delivery speed and accuracy as they are invisible to customers.
- Cost savings: Inventory can be made easy to store, find, retrieve, and ship with a well-organized warehouse, which in turn help save your business the cost of extra labor and work hours.
- Smoother supply chain: Warehouse management help ensure orders enter faster, leave quickly, and optimize warehouse space across the supply chain.
What is a Warehouse Management System?
Warehouse management is a significant commitment, and it becomes even more complex as a business expands. Efficient warehousing can be achieved by supporting warehouse managers and staff with warehouse management systems (WMS). These systems involve both software and hardware tools that ensure smooth warehouse operations. When used exclusively online, warehouse management software or inventory management software is referred to as WMS. These tools help simplify warehousing and fulfillment tasks.
While WMS can function as a standalone product that simplifies and optimizes warehouse management, it is often included as part of a larger enterprise resource planning (ERP) suite. WMS adds value to the warehousing process by offering real-time visibility into inventory levels and locations, using data analytics and automation to forecast demand and sales, leveraging artificial intelligence (AI) to optimize daily operations, providing step-by-step instructions for staff, and monitoring performance to offer an overview of operations health and potential issues.
The demand for WMS has surged, particularly due to the rise of e-commerce. These systems enable companies to scale their warehouse operations efficiently in response to increasing demand. As customers expect faster deliveries, high-quality WMS is crucial to meeting those expectations.
Primary Warehouse Management Processes:
Inventory tracking:
Inventory tracking involves monitoring and regularly updating stock levels. It is essential for businesses to know the availability of items in the warehouse, their storage locations, and when they need to be replenished.
This step in warehouse management offers complete visibility into your inventory, ensuring that staff are aware of the exact status of specific products. Inventory tracking is also crucial for managing supplies from vendors, allowing businesses to monitor the location and availability of incoming goods.
With proper inventory tracking, it becomes easier to understand the movement of products in and out of the warehouse. This enables employees to quickly determine the quantity of products available for orders and when restocking is necessary. Additionally, inventory tracking aids in demand forecasting. As your business grows, maintaining inventory accuracy becomes increasingly critical.
Receiving and stowing:
Picking and packing:
- Zone picking: Zone picking works best for sellers with items commonly stored and ordered together as specific items will be picked from the same zones by warehouse staff.
- Discrete picking: Discrete picking is best suited for small stores as any particular order is not followed in it. Mostly your staff walk through the warehouse and select items.
- Wave picking: Wave picking is same as discrete picking. But, it only happens at specific intervals. So, the workers will be able to spend the rest of their time on other tasks.
- Batch picking: All the items are simultaneously picked in a specific group of orders by warehouse staff.
Shipping:
Reporting:
Once orders are packed, shipped, and successfully delivered, itâs essential to take stock and update your inventory. Key performance indicators (KPIs) such as total orders shipped, accuracy, efficiency, and more will be reported.
Warehousing software is typically used by companies to ensure transparency in tracking these KPIs. The software also records returns caused by mis-picks, mis-packs, or damaged items, helping identify the source of errors. While human mistakes are inevitable in any fulfillment operation, a well-implemented warehouse management system (WMS) can significantly reduce them.
Warehouse processes are interconnected. For instance, the shipping process is heavily influenced by packing, and neither picking nor packing can run smoothly without proper storage. By planning and optimizing each step, you can improve overall outcomes and streamline the entire process.
Best Practices for Warehouse Management:
Warehouse Management System (WMS):
Warehouse management software (WMS) is essential for optimizing warehouse operations. It helps save space, reduce labor costs, and streamline processes. Many warehouses are adopting WMS due to the significant value it provides, with trends in robotics and AI pointing toward a smarter, more efficient inventory management system.
Cloud Storage:
Forward-thinking sellers are migrating their warehouse operations to the cloud, integrating technology to support their processes. Cloud computing offers substantial benefits in terms of data storage, accessibility, and support. By using cloud services, businesses can eliminate the need for on-premises data storage and dedicated IT teams, saving costs and paying only for the storage they use.
Data Collection Technology:
To replace manual record-keeping, sellers are implementing data collection technologies like barcodes, RFID, and SKUs. These technologies automate the tracking of inbound and outbound stock, enhancing visibility, accuracy, and efficiency while reducing human error.
Automation:
Automating various warehouse management processes increases efficiency and reduces time. Tasks such as stock placement, retrieval, and packing can be handled by automated workflows. Robotics and conveyor belts can assist in picking and delivering items, reducing the need for manual labor and speeding up operations.
Hands-Free Picking:
Automated picking allows workers to call up identified items quickly using touch screens or voice-picking tools. With wrist-mounted or handheld units, staff can select and retrieve items more efficiently, improving turnaround times and increasing warehouse throughput.
Wave Planning:
Wave planning helps optimize picking routes and reduces time spent searching for items. By consolidating picking efforts into the most efficient routes, wave planning enhances productivity. Itâs especially beneficial for small businesses looking to streamline their picking process.
Touch Minimization:
Minimizing touch points in the warehouse reduces the risk of damage, dirt, or mishandling, ensuring greater integrity of the process. By reducing unnecessary handling, companies can accelerate fulfillment and avoid redundant steps like shelf returns.
Cycle Counting:
While WMS tracks inventory levels, cycle counting is important for reconciling inventory figures and ensuring accuracy. Instead of relying on infrequent physical counts, cycle counting spreads out the process, helping maintain accurate stock levels without causing disruption.
Warehouse Safety:
Effective warehouse management goes beyond stock control; it also involves ensuring worker safety. Providing the necessary safety equipment and health measures is crucial to avoid workplace injuries, which can halt operations and create delays.
Standardized Vendor Operations:
Managing suppliers effectively can lead to significant cost savings and increased efficiency. By coordinating delivery times, packaging, and locations, businesses can ensure that supplies arrive when needed, reducing disruptions in the supply chain.