Flexible manufacturing system
Updated: November 20, 2024
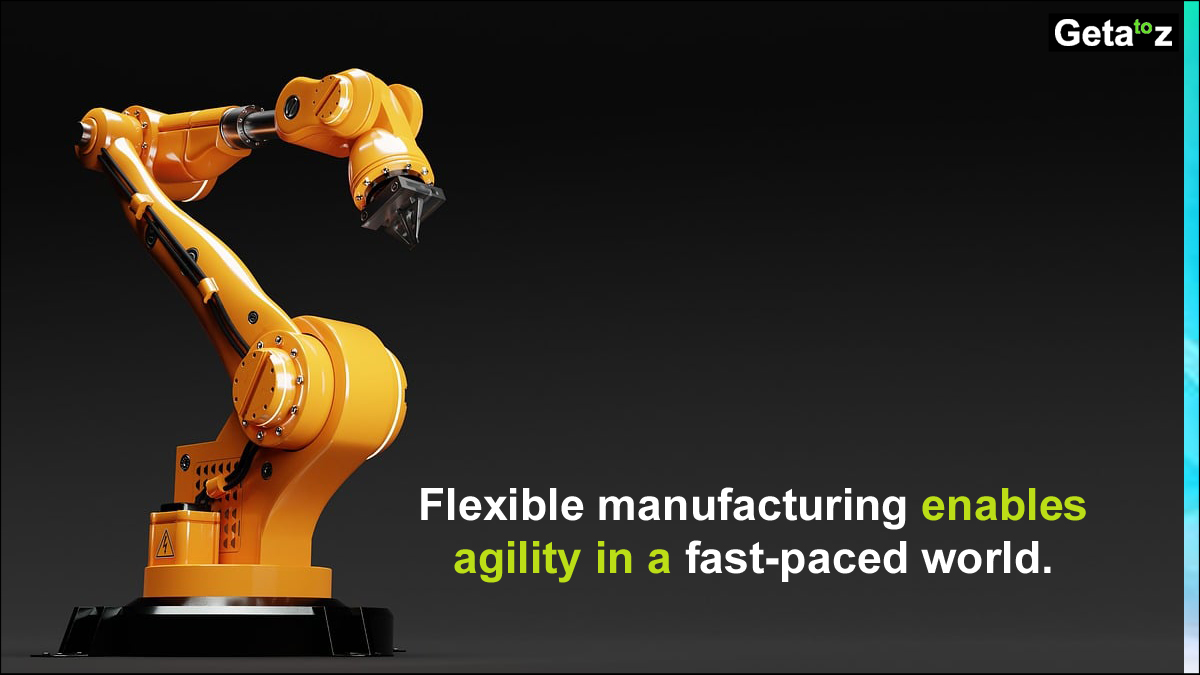
What is a Flexible Manufacturing System?
Flexibility in Flexible Manufacturing:
Flexible manufacturing systems (FMS) rely on two key categories of flexibility to adapt to changing production needs: Machine Flexibility and Routing Flexibility.
1. Machine Flexibility
Machine flexibility refers to a machine's ability to adapt to the production of new product types by altering the sequence of operations performed on a specific part.
- Key Features:
- Enables rapid adaptation to new or modified product designs.
- Emphasizes the utility and versatility of machines in agile production environments.
- Critical for industries where frequent changes in design or product variety are common.
This type of flexibility ensures that manufacturing processes can efficiently accommodate dynamic product demands without significant downtime or equipment replacement.
2. Routing Flexibility
Routing flexibility measures the extent to which the system can adapt to variations in production capacity, volume, or product variety.
- Key Features:
- Allows tasks to be performed on alternative machines, ensuring continuity even if specific equipment is unavailable.
- Adapts to fluctuations in raw material availability or shifts in order volumes.
- Ensures operational uptime and reduces production disruptions by providing multiple pathways for task completion.
This flexibility is crucial for maintaining smooth operations in environments with variable demands or resource constraints.
Types of Flexible Manufacturing Systems:
- Sequential FMS: One part is typically produced before moving on to another in a sequential FMS. It is used in several manufacturing processes.
- Random FMS: Machines that can handle different product specification are used in Random FMS and all are then created at once in random order.
- Dedicated FMS: A small variety of parts or goods is created over an extended period in Dedicated FMS as it works at a comparatively rapid rate.
- Engineered FMS: Although an engineered flexible manufacturing system is similar to a dedicated FMS, some pieces would be manufactured continually in an engineered FMS.
- Modular FMS: The most significant degree of flexibility is provided in Modular FMS. The operator can to switch between sequential, random, dedicated and designed FMS modes following the demands of the manufacturing process in this system.
Working of Flexible Manufacturing System:
1. Processing Stations
Processing stations are the heart of production in an FMS, performing the actual manufacturing tasks.
- Typically, multiple machines are included in a single FMS, connected by conveyors or autonomous guided vehicles (AGVs).
- Depending on the system's flexibility, these machines can produce either a single product or a variety of items simultaneously.
- A fully integrated system of processing stations can function as an automated factory, significantly reducing human intervention.
2. Automated Material Handling and Storage Systems
Automated material handling and storage systems ensure smooth material flow throughout the production process.
- Materials are fed into an automated storage system (or loader) at one end of the conveyor or AGV.
- Pick-and-place robots distribute these materials to the appropriate machines for processing.
- Finished products are retrieved through the unloader at the other end, completing the automated workflow.
3. Central Control Computers
A central control computer manages all operations in the FMS, minimizing the need for onsite human intervention.
- This system coordinates the activities of processing stations and material handling systems.
- It optimizes processes, reduces downtime, and ensures consistent production quality.
Real-World Applications of FMS
Jewelry Manufacturing:
FMS is widely used in creating custom jewelry, an industry that demands precision and adaptability.
- Jewelry production involves six key steps: 3D modeling, wax modeling, casting, assembly, stone setting (if needed), and polishing.
- Each step can be performed on separate machines, while tasks like loading, unloading, and stone setting can be automated through the central control system.
- FMS allows manufacturers to adapt quickly to design variations, production volumes, and new product requirements, boosting market competitiveness.
Household Equipment Manufacturing:
FMS is extensively used by manufacturers of household appliances such as refrigerators, stoves, dishwashers, and washing machines.
- It enables the production of high-quality, metal-based components or entire appliances with reduced production time.
- FMS also facilitates efficient manufacturing of everyday items like wiring, utensils, foil paper, nails, rods, gates, and statues.
FMS vs. Flexible Manufacturing Cells (FMCs)
FMS is often compared to Flexible Manufacturing Cells (FMCs), but the two differ in complexity.
- FMS is categorized as an autonomous system, featuring sophisticated monitoring and diagnostic capabilities within its central control systems.
- FMCs are simpler systems and lack the advanced integration and automation of FMS.
Global Adoption of FMS
Flexible manufacturing systems are a cornerstone for global manufacturers aiming to improve agility and efficiency. By implementing FMS, businesses can optimize operations, reduce production times, and adapt to market demands, ensuring a competitive edge in industries that require precision and flexibility.
Key features of a Flexible Manufacturing System:
Advantages of using a Flexible Manufacturing System:
1. Flexibility
FMS provides both machine flexibility and routing flexibility, enabling companies to adjust to volatile market conditions and reduce production risks. The system can easily accommodate changes in product types, volumes, and production schedules.
2. Improved Quality and Reduced Waste
By utilizing advanced, robust machines, FMS ensures consistent manufacturing across processes with minimal human intervention. This leads to higher-quality products with fewer defects. Additionally, the production process generates less waste and scrap, resulting in improved efficiency. The consistency and precision of FMS also support agile manufacturing, giving companies an edge over competitors.
3. Cost-Effectiveness
FMS helps reduce both manufacturing and operational costs. With the ability to replace multiple machines with a single system, the need for additional equipment and plant space is minimized. Moreover, the automation of tasks reduces labor requirements, allowing businesses to lower personnel costs while maintaining high production output.
4. Increased Productivity
Flexible manufacturing systems boost productivity by minimizing downtime. Production lines do not need to be shut down or reconfigured when switching between different products, ensuring continuous output and higher efficiency.
5. Adaptability to Changes in Production Volume and Mix
FMS is highly adaptable, easily adjusting to fluctuations in product volumes, mixes, or the introduction of new products. This flexibility allows businesses to respond swiftly to market demands or shifts in customer preferences without disrupting the production flow.
6. Shortened Production Lifecycle
FMS accelerates the production process by efficiently distributing materials across machines with high speed and accuracy. This leads to a shortened product lifecycle, reducing the time from design to finished product and enabling faster time-to-market.
In summary, FMS enhances manufacturing efficiency, quality, and flexibility while reducing costs and waste, providing a significant competitive advantage for companies across various industries.
Disadvantages of using a Flexible Manufacturing System:
1. High Capital Investment
Adopting an FMS requires a significant capital investment, which can be a major barrier, especially for companies with tight cash flows. The initial cost of purchasing the system, along with ongoing maintenance expenses, can be unaffordable for many businesses.
2. Difficulty in Adoption
Implementing an FMS is a complex process that requires careful planning and can limit future changes. It demands significant time and resources to ensure proper system configuration, scheduling, and integration with existing processes. The transition to FMS can also involve altering the entire manufacturing process, which can be a challenging task for many companies.
3. Considerable Development Time
The planning and scheduling process for setting up a flexible manufacturing system is time-intensive. Rushing through the development phase may result in a system that is ill-suited for the company's specific needs, reducing its effectiveness and potential benefits.
4. Additional Training Costs
While FMS reduces the need for human labor, it requires highly skilled personnel to manage and maintain the system. This necessitates additional training costs, as employees must be equipped with the knowledge and expertise to operate and troubleshoot the system effectively.
In conclusion, these challenges must be addressed to ensure the successful implementation of FMS and to achieve the desired operational improvements.